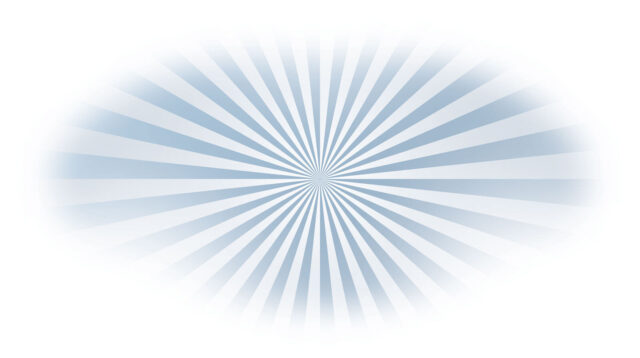
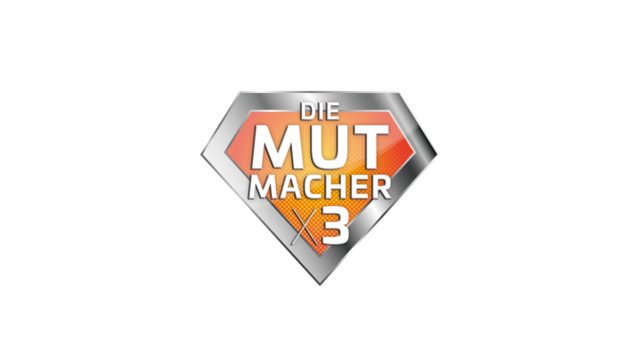
Diese drei Unternehmen haben das Beste aus der Corona-Krise gemacht – und sich dafür ein Stück weit selbst neu erfunden. Drei Geschichten von Mut, Glücksgriffen und Erfindergeist in der Pandemie.
Reise in die virtuelle Welt statt ins Gefängnis
Die Quarantänebeschränkungen verlangen Lanico, dem Hersteller von Maschinen für Verpackungsmaterial, viel ab. Doch Not birgt auch Chancen.
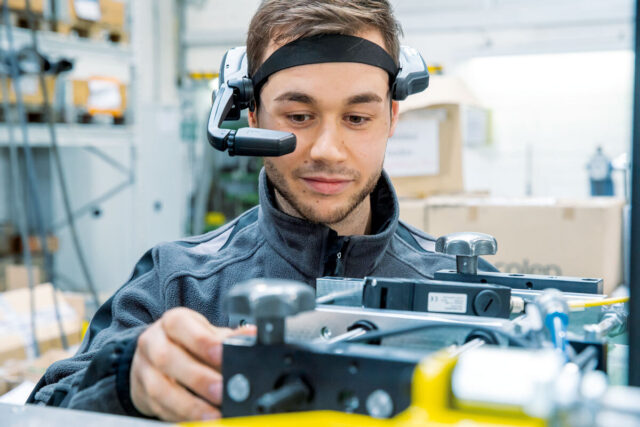
Fotos (2): Axel Herzig
Bei Indonesien war für Wolfgang Niemsch schließlich Schluss. Bisher hatte der Chef von Lanico in Braunschweig es seinen Servicetechnikern freigestellt, ob und in welche Länder sie trotz Reise- und Quarantänebeschränkungen wegen der Coronapandemie reisen, um die Fertigungsmaschinen in Betrieb zu nehmen, zu warten oder zu reparieren. Und bisher hatten die Mitarbeiter immer praktische Lösungen gefunden.
Sie flogen mit Ausnahmegenehmigung in die USA, als Ex-US-Präsident Donald Trump verkündete, kein Nicht-US-Bürger käme mehr ins Land. Sie fuhren mit dem Auto nach Mailand, als Flüge von Norddeutschland nach Norditalien zwischenzeitlich eine kleine Weltreise waren. Und sie wechselten sich in Frankreich als Team ab, weil man sich maximal 72 Stunden in einem anderen EU-Land aufhalten darf, ohne in Quarantäne zu müssen. „Der Service für unsere Maschinen ist seit gut einem Jahr sehr herausfordernd“, sagt Niemsch. „Es kostet viel Zeit, es gibt viele Hürden und es ist immer ein Risiko dabei.“ Deshalb bemühten sich Lanico und die Kunden, den Aufwand möglichst klein zu halten und einen Techniker nur noch loszuschicken, wenn massive Probleme in der Produktion drohen.
Quarantäne im Gefängnis
So etwa kürzlich, als in Indonesien eine wichtige Fertigungsanlage eintraf, die in Betrieb genommen werden musste. Doch angesichts der Quarantäneregelungen war Niemsch entsetzt: „Jeder, der dort einreist, muss für zwei Wochen in Quarantäne – und zwar in einem ehemaligen Gefängnis.“ Er versuchte, eine Alternative auszuhandeln, ein Hotel auf Bali, in dem die Mitarbeiter bleiben konnten. „Die Kosten waren in diesem Moment nicht wichtig. Hauptsache, die Techniker mussten nicht in diesen fürchterlichen Knast.“ Doch die indonesische Verwaltung blieb hart: Entweder Gefängnis oder keine Einreise.
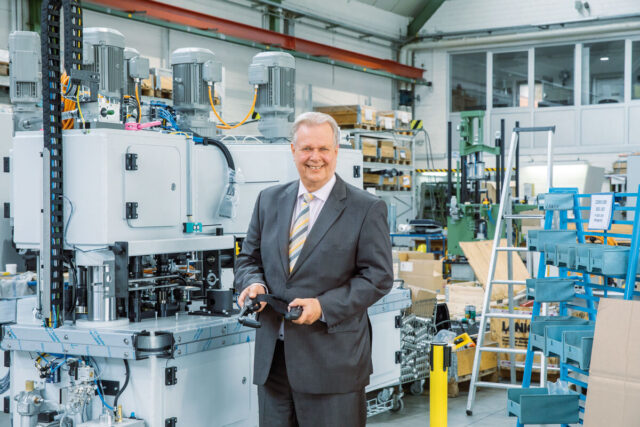
Von der Not zur Chance: Durch die Krise hat Lanico wertvolle Erfahrungen mit VR-Technik gesammelt.
Natürlich flog niemand nach Indonesien. Doch das Grundproblem blieb: Die Maschine musste in Betrieb genommen werden. Da kamen die Mitarbeiter auf eine Idee: Warum es nicht digital versuchen? Schon seit Monaten tüftelten sie daran, eine Maschinenbesichtigung mithilfe von Virtual Reality zu konstruieren. Dieses Wissen wurde jetzt nützlich. Glücklicherweise hatte Lanico die Maschine vor dem Verschiffen mit einer Drohne aus allen möglichen Winkeln fotografiert. Diese Bilder wurden die Grundlage für ein individuelles Virtual Reality-Programm.
Kompliment an Mitarbeiter
„Ein Mitarbeiter der Firma vor Ort setzte sich die Brille auf und unsere Techniker saßen hier vor dem Computerbildschirm und leiteten ihn Schritt für Schritt an“, berichtet Niemsch mit Stolz in der Stimme. Abgesehen von ein paar Schwierigkeiten mit der Datenübertragung klappte alles überraschend reibungslos. „Ein großes Kompliment an die Mitarbeiter für diese Leistung. Das macht Mut, dass wir mit VR in Zukunft noch viel mehr probieren können.“
Kein Segment mehr als 30 Prozent
Wenn es richtig gut läuft, läuten bei Andreas und Gerd Röders die Alarmglocken. Warum gerade das sie bisher in jeder Krise gerettet hat.
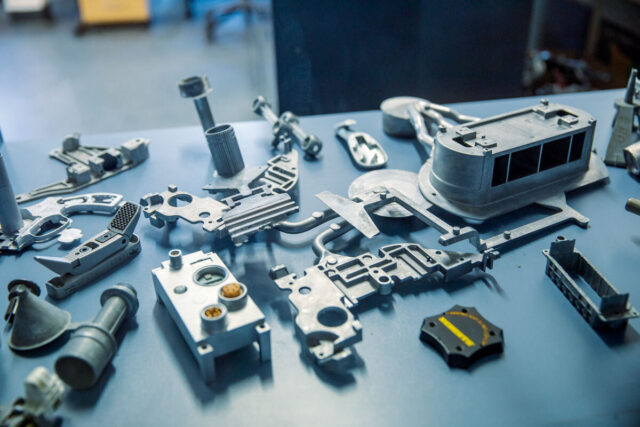
Fotos (2): Axel Herzig
In den 60er Jahren kam die erste Krise. Japanische Kameras eroberten den Markt und verdrängten die deutsche Fotoindustrie nahezu komplett. „Unser Unternehmen hat 60 Prozent des Umsatzes mit Kameragehäusen erwirtschaftet“, erinnert sich Andreas Röders, Geschäftsführer der G.A. Röders GmbH, einem Spezialisten für Druck- und Spritzguss, mit Sitz in Soltau. Das Unternehmen war damals fast pleite. Und traf eine Entscheidung: Kein Kunde sollte so groß werden, dass eine existenzielle Abhängigkeit entsteht. „Wir haben uns verordnet, in einem Segment maximal 30 Prozent Umsatz zu generieren“, so Röders.
Raus aus der Erfolgsbox
Klar, die Automobilindustrie sei ein wichtiges Standbein des Unternehmens. „Und doch haben wir versucht, auch dieses Segment nicht zu groß werden zu lassen“, bestätigt Gerd Röders, Partner im familiär geführten Betrieb. Man müsse zwingend raus aus der Erfolgsbox, auch wenn es dort verdammt angenehm sei. „Wir wollen die Veränderung meistern, bevor sie uns trifft“, erklären die Röders ihr Vorgehen.
Das Unternehmen wurde zum Prozessspezialisten. Im Grunde ist die Sache einfach: Die Techniker aus Leidenschaft entwickeln einen innovativen Prozess und verkaufen ihn an so viele Segmente wie möglich. So habe man schon vor einiger Zeit auch Gussteile an Kunden der Medizintechnik verkauft. Die Rahmen der komplexen Geräte seien schließlich aus Aluminium. Ein Schachzug, von dem das Unternehmen, als das Geschäft in der Automobilindustrie pandemiebedingt einbrach, profitierte. Denn jetzt waren Beatmungsgeräte die Umsatztreiber.

Andreas und Gerd Röders (v.l.) Geschäftsführer der G.A. Röders GmbH, setzen immer auf mehrere Produkte und Märkte.
Neue Ideen brauchen Impulse. So arbeitet das Unternehmen in zahlreichen Verbänden und Initiativen. Gemeinsam mit der TU Braunschweig realisieren die Guss-Spezialisten regelmäßig Forschungsprojekte. Damit genügend Kapazität zum freien Denken da ist, haben die Röders extra zwei Entwicklungsingenieure eingestellt. Und am Ende kommt er heraus, der eigene Ofen, mit dem das Unternehmen seinen Kunden zwölf verschiedene Legierungen anbietet. Das könne kaum jemand.
Plötzlich ist da ein Riesen-Markt
Die Legierung war es auch, die die Tür zum Bereich „Autonomes Fahren“ aufstieß. „In jedem Selbstfahrer-Auto sind 25 Kameras und 90 Steuergeräte“, erzählt Andreas Röders. Die üppige Elektronik sorge für eine besonders hohe Wärmeentwicklung. Man brauchte Kühlkörper, diese seien oft aus Guss gefertigt. „Jetzt kommt der Kunde und braucht eine besonders leitfähige Legierung“, beschreibt Röders den Prozess. „Dann fangen wir an. Wir reden. Und probieren gemeinsam aus.“ Die Guss-Experten finden die passende Legierung und werden damit zum Spezialisten für Kühlkörper. Ein neuer Riesen-Markt tut sich auf.
Die Spezialisten für den Kampf gegen Corona
Global Player, Membranfilterpionier, Biopharmaexperte: Die Liste an Beschreibungen für das Göttinger Traditionsunternehmen Sartorius könnte beliebig fortgesetzt werden. In den vergangenen zwölf Monaten ist noch ein weiteres Attribut hinzugekommen: Coronavirus-Bekämpfer.
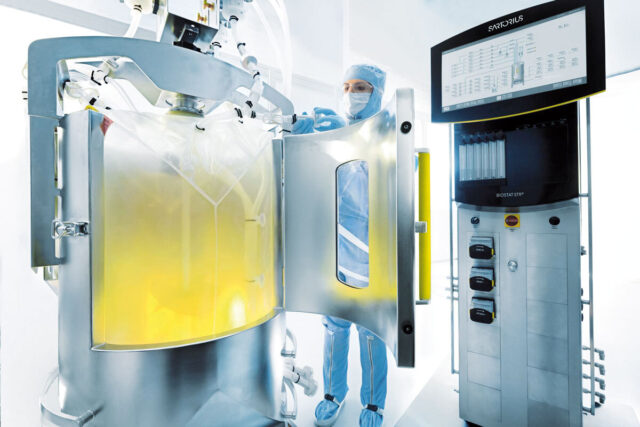
Fotos (2): Sartorius AG
„Wir sehen uns in dieser Pandemie als Teil der Lösung und tragen mit unseren Technologien maßgeblich dazu bei, dass Impfstoffe gegen das Coronavirus in großem Maßstab hergestellt werden können“, erklärt Pressesprecher Timo Lindemann und hält fest: „Deshalb arbeiten wir eng mit allen relevanten Impfstoffherstellern zusammen.“
Diese Zusammenarbeit klappt auch deshalb so reibungslos, weil Sartorius sich mit Forschung und Industrie im biopharmazeutischen Bereich exzellent auskennt. Sein großes Know-how brachte das südniedersächsische Unternehmen zum Beispiel entscheidend in den Aufbau des Werks von Biontech in Marburg ein. „Von uns stammt ein Großteil der Produktionstechnologien, um dort Corona-Impfstoff herzustellen“, sagt Lindemann.
Doch wie sieht das im Detail aus? Herzstück ist ein Bioreaktor aus Edelstahl, in den ein steriler Einmalbehälter aus Kunststoff gesetzt wird. „In den Behälter kommen Zellen, die den Wirkstoff produzieren und sich dort unter optimalen Bedingungen vermehren“, beschreibt Timo Lindemann den Prozess, der nach einem definierten Zeitpunkt in die Filterung und Aufreinigung der Zellsuppe mündet. „Das bedeutet, dass der Wirkstoff von anderen Stoffen getrennt wird“, so Lindemann.
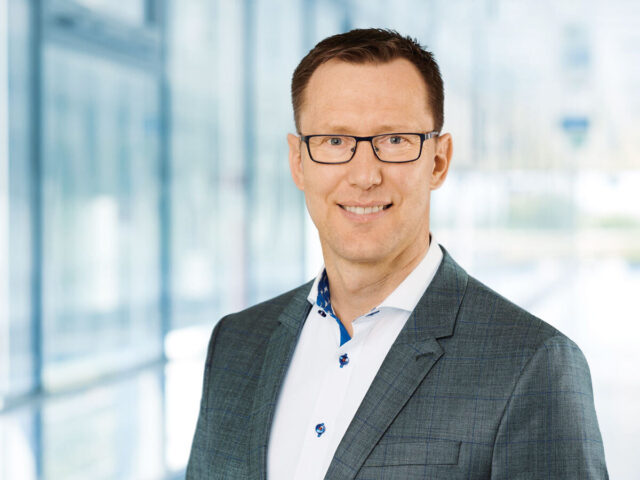
Die Technik für den Erfolg: Mit seinen Produkten wirkt Sartorius maßgeblich an der Herstellung von Corona-Impfstoffen mit, diesen Zusammenhang betont Pressesprecher Timo Lindemann.
Membrane für Corona-Tests
Die Filter- und Chromatografielösungen hierfür liefert ebenfalls Sartorius. Und: Der Göttinger Konzern hat die Fachkräfte im Marburger Werk extra geschult. In Sachen Virusbekämpfung ist das aber noch nicht alles: Von Sartorius produzierte Membrane werden auch für Corona-Tests benötigt.
Klingt so, als ob die Biopharmaprofis dafür extra Fachwissen aufbauen und Produkte neu auf den Markt bringen mussten. „Das ist nicht der Fall. Alle Komponenten, die jetzt zum Einsatz kommen, stellen wir seit Jahren, teilweise Jahrzehnten her, um die Entwicklung und Produktion von Medikamenten und anderen Impfstoffen zu unterstützen“, macht Lindemann deutlich. Membrane beispielsweise sind auch Bestandteil anderer Diagnostiktests wie etwa Schwangerschaftstests. Der große – und weltweite – Bedarf am Sartorius-Angebot hat dazu geführt, dass der Umsatz im vergangenen Jahr kräftig gewachsen ist – um rund 30 Prozent auf 2,34 Milliarden Euro. „Circa 14 Prozentpunkte davon lassen sich der Pandemie zuschreiben. Wir wären also auch ohne die Pandemie deutlich gewachsen“, unterstreicht Timo Lindemann.